Revolutionizing Water Purification with 3D Printing Technology
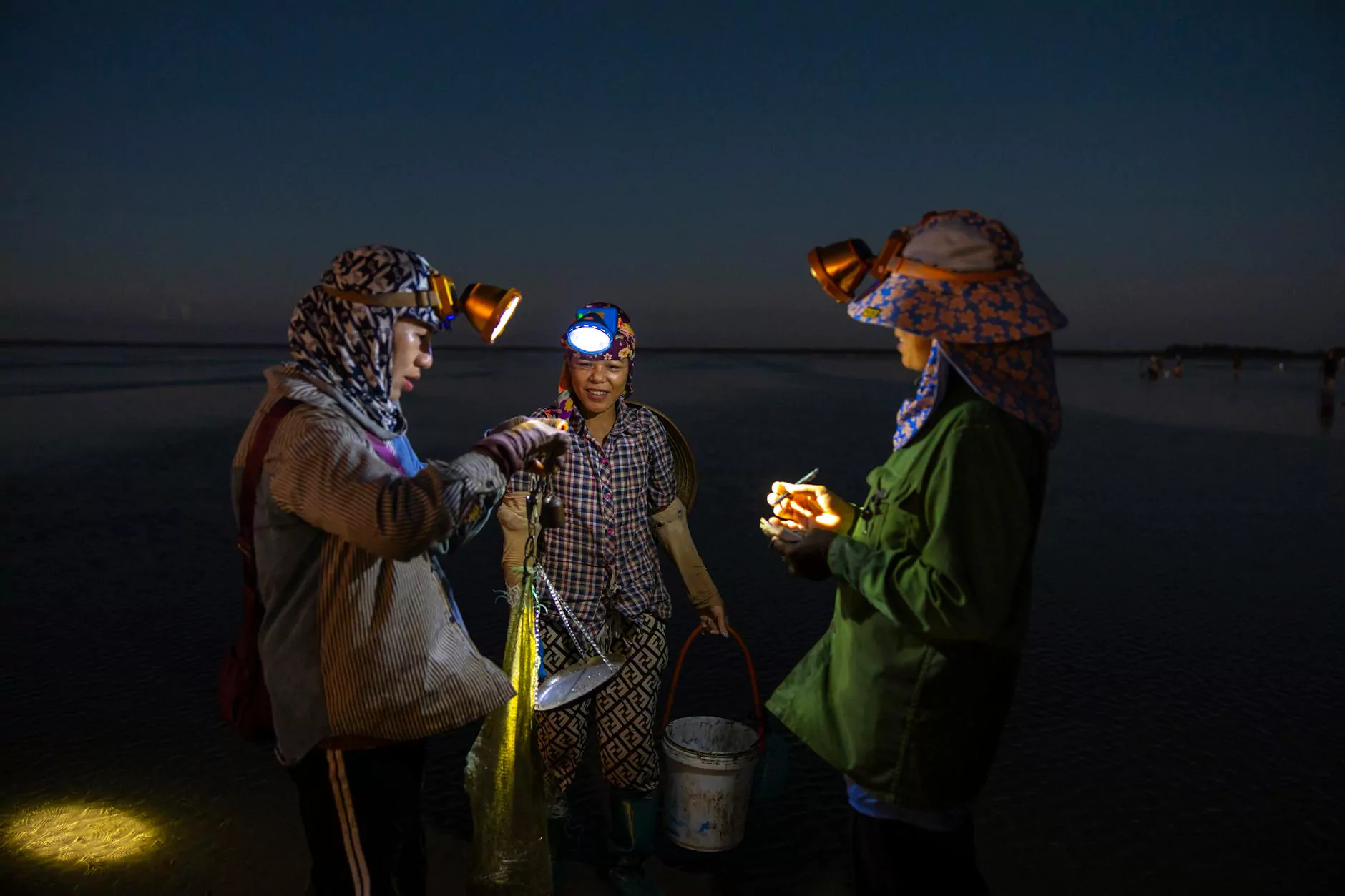
In today's rapidly evolving industrial landscape, 3D printing has emerged as a transformative technology, redefining how we approach manufacturing, innovation, and sustainable development. Among its numerous applications, the development of 3d printed water filters stands out as a game-changer, offering unprecedented customization, efficiency, and eco-friendliness in the realm of water purification. This comprehensive exploration delves into the transformative role of 3D printing in creating advanced water filtration systems, highlighting its benefits, innovative techniques, and future potential.
Understanding 3D Printing and Its Impact on Industry
3D printing, also known as additive manufacturing, is a process where objects are built layer-by-layer from digital designs. This method allows for the creation of complex geometries and highly customized products that traditional manufacturing methods often struggle to produce efficiently. Its adaptability and precision make it ideal for producing specialized components like water filters that require intricate internal structures to optimize filtration performance.
In industries ranging from aerospace to healthcare, 3D printing has demonstrated its capacity to innovate and reduce costs. When applied to the water treatment sector, it allows engineers and designers to tailor filtration devices to specific contaminants, flow rates, and usage environments, paving the way for more effective and sustainable water purification solutions.
The Rise of 3d Printed Water Filters: A Sustainable Solution
Access to clean water remains a critical challenge worldwide. Traditional filtration systems often involve costly manufacturing, limited customization, and environmental concerns related to waste and materials. However, the advent of 3d printed water filters addresses many of these issues, underpinning a shift toward more sustainable, affordable, and adaptable water purification options.
3D printing technology enables the production of highly precise filters with complex internal structures that maximize surface area and filtration efficiency. Moreover, it facilitates rapid prototyping, allowing the development of innovative filter designs that can target specific pollutants such as heavy metals, microplastics, bacteria, and viruses.
The environmental benefits are substantial. Using eco-friendly materials and minimizing waste during manufacturing, 3d printed water filters can be produced with minimal ecological footprint compared to traditional methods. Additionally, the ability to produce filters on-demand reduces inventory waste and transportation emissions, aligning with modern sustainability goals.
Design Flexibility and Customization in 3D Printing Water Filters
One of the most compelling advantages of 3D printing in creating water filters is the unparalleled level of design flexibility. Engineers can craft filters with intricate geometries that enhance flow dynamics, increase contact time with contaminants, and improve overall system efficiency. For instance, lattice structures and porous materials can be optimized for specific filtration needs, whether for household use, industrial applications, or portable devices.
- Tailored pore size: Design filters with precise pore sizes to target specific impurities.
- Optimized flow channels: Create internal flow pathways that reduce pressure drops and prevent clogging.
- Multi-material integration: Combine different materials within a single print to add functionalities such as antimicrobial properties or increased durability.
- Rapid iteration: Quickly prototype and modify designs, accelerating innovation cycles.
The customization potential ensures that water filters can be customized for different environments—from remote rural areas needing simple filtration solutions to industrial settings requiring high-capacity, multi-stage filtration systems.
Materials Used in 3D Printing of Water Filters
The selection of materials is crucial for producing effective 3d printed water filters. Factors such as biocompatibility, chemical resistance, mechanical strength, and porosity determine the longevity and performance of the final product. Common materials include:
- ABS (Acrylonitrile Butadiene Styrene): Durable, resistant to impact and chemicals, suitable for robust filters.
- PLA (Polylactic Acid): Biodegradable, environmentally friendly, ideal for disposable or short-term filters.
- Resins: Used in SLA (Stereolithography) printers, offering high resolution and smooth surfaces, beneficial for fine filtration structures.
- Specialty Filtration Materials: Incorporating activated carbon, ceramic, or nanomaterials during printing to enhance filtration efficacy.
Research into composite materials and bio-based options continues to expand the possibilities for 3d printed water filters, with innovations focused on increasing antimicrobial properties and improving the removal of a broader spectrum of contaminants.
Manufacturing Process of 3D Printed Water Filters
The creation of 3d printed water filters typically involves several key steps:
- Design: Using CAD software to develop complex filter geometries tailored to specific needs.
- Material selection: Choosing appropriate printable materials based on desired properties.
- 3D printing: Utilizing technologies such as FDM, SLA, or SLS to produce precise filter components.
- Post-processing: Removing support structures, surface finishing, and sometimes sterilization or functionalization of the filter surfaces.
- Validation and Testing: Conducting water flow and filtration tests to ensure performance standards are met.
This flexible manufacturing approach allows prototypes and production runs to be completed rapidly, reducing time-to-market and enabling iterative design improvements.
Applications and Benefits of 3D Printed Water Filters
The scope of 3d printed water filters extends across various sectors, offering transformative benefits:
- Municipal Water Treatment: Customizable filters that adapt to local water quality challenges.
- Emergency Response and Disaster Relief: Portable, easily deployable filters for affected populations.
- Industrial Filtration: High-capacity, durable filters tailored for specific contaminants in manufacturing processes.
- Personal Water Devices: Compact, ergonomic filters suitable for outdoor activities or travel.
Key benefits include:
- Cost-effectiveness: Reduced manufacturing and logistics costs.
- Rapid customization: Design adjustments to meet unique needs.
- Sustainability: Use of eco-friendly materials and minimized waste.
- Efficiency: Enhanced filtration performance through complex geometries and multifunctionality.
Challenges and Future Directions in 3D Printing of Water Filters
Despite the promising potential, several challenges persist in the widespread adoption of 3d printed water filters:
- Material limitations: Need for more specialized, durable, and food-safe materials suitable for water contact.
- Scaling production: Transitioning from prototypes to mass production while maintaining quality.
- Regulatory standards: Ensuring compliance with health and safety regulations in different markets.
- Longevity and maintenance: Developing filters with lifespan guarantees and easy cleaning or replacement parts.
Looking ahead, advancements in multi-material 3D printing, nano-engineered materials, and smarter designs incorporating sensors and IoT connectivity promise to redefine water filtration technology. The integration of smart filters can enable real-time monitoring of water quality, providing immediate feedback and improving user safety.
Additionally, collaborative efforts between researchers, industry leaders, and policy-makers will accelerate innovation, standardization, and accessibility, ensuring clean water becomes a reality for underserved communities worldwide.
The Business Opportunity: Harnessing 3D Printing for Water Treatment Industry Growth
For businesses in the 3D printing sector, especially those specializing in the industry category like 3dprintwig.com, there lies a tremendous opportunity to develop custom 3d printed water filter solutions. By leveraging cutting-edge design and manufacturing capabilities, industry players can enter a growing market with high demand for innovative, sustainable, and affordable water filtration systems.
Strategic steps include:
- Investing in advanced 3D printing technologies such as metal and biocompatible resin printers.
- Developing a portfolio of customizable filter designs tailored for various sectors.
- Partnering with water treatment companies and NGOs to create solutions for global challenges.
- Focusing on eco-friendly materials to enhance brand reputation and comply with environmental regulations.
As the demand for clean water solutions accelerates, establishing expertise in this niche can position a company as an industry leader and pioneer in 3D printed water filtration innovations.
Conclusion: Embracing the Future of Water Purification with 3D Printing Innovation
The evolution of 3D printing technology offers unparalleled opportunities in designing, manufacturing, and deploying highly effective water filters. By harnessing the power of additive manufacturing, industry leaders and entrepreneurs can deliver customized, sustainable, and cost-efficient solutions that address global water quality challenges effectively.
The future of water purification is undeniably intertwined with 3D printing. Continuous research, innovative material development, and strategic collaborations will drive this transformation forward, providing access to safe drinking water for communities worldwide and creating new business opportunities for those ready to innovate.