Understanding Injection Molded Plastic Manufacturers: A Comprehensive Guide
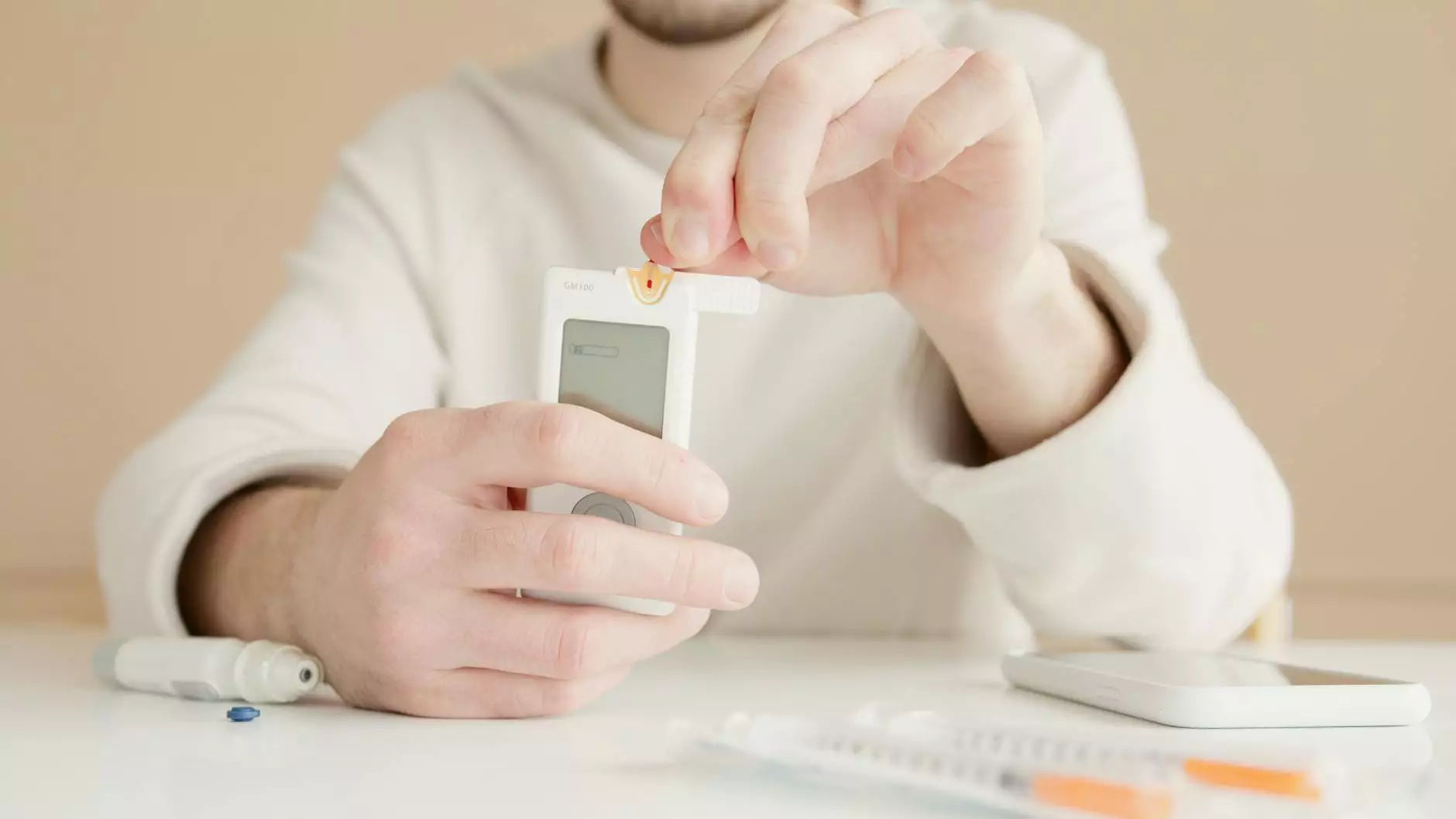
Injection molded plastic manufacturers play a crucial role in modern manufacturing. Their ability to produce high-quality plastic components quickly and efficiently makes them indispensable across numerous industries. In this in-depth article, we will explore the nuances of injection molding, the advantages of working with these manufacturers, and the impact of their products on the market. By the end, you will have a thorough understanding of the significance of injection molded plastics.
What is Injection Molding?
Injection molding is a manufacturing process used to create parts by injecting molten material into a mold. This technique is predominant in the production of plastic components, making it a staple in many industries. The process involves several key steps:
- Material Preparation: Raw plastic material, usually in the form of pellets, is fed into a hopper.
- Melting: The pellets are heated in a barrel until they reach a liquid state.
- Injection: The molten plastic is injected into a mold at high pressure.
- Cooling: The plastic is allowed to cool and solidify, taking the shape of the mold.
- Demolding: The solid part is ejected from the mold.
The entire process is efficient, enabling manufacturers to produce thousands of identical products in a short amount of time. This efficiency is what drives many businesses to partner with injection molded plastic manufacturers.
The Advantages of Injection Molding
1. Cost-Effectiveness
One of the main reasons businesses turn to injection molded plastic manufacturers is the cost-effectiveness of the process. Once the initial mold is created, the cost per unit is significantly lower when compared to other manufacturing methods. This is especially beneficial for large production runs.
2. Product Consistency and Quality
The injection molding process ensures that each part produced is consistent in quality and dimensions. This reliability means that businesses can develop products that meet exact specifications, reducing waste and improving overall quality control.
3. Versatility of Materials
Injection molding is compatible with a variety of plastics, including thermoplastics and thermosetting plastics. This versatility allows manufacturers to tailor materials to fit specific applications, whether they require strength, elasticity, or thermal resistance.
4. Complex Geometries
Injection molded plastic manufacturers can produce intricate designs that may be difficult or impossible to achieve with other methods. This capability opens up new possibilities for product design, enabling the creation of components with complex shapes and features.
5. Reduced Labor Costs
Automation is a significant component of the injection molding process. Automated systems reduce the need for extensive manual labor, further driving down production costs. This allows companies to allocate resources more effectively.
Industries Benefiting from Injection Molding
The benefits of injection molding are seen across various industries, helping them design and manufacture products that meet specific market needs:
1. Automotive Industry
The automotive industry utilizes injection molded plastics for parts such as dashboards, door panels, and bumpers. These components must be durable and lightweight, making injection molding an ideal choice. The ability to create high-volume components quickly aligns perfectly with the fast-paced automotive demands.
2. Electronics
In electronics, injection molded components are ubiquitous. From casings for devices to intricate internal parts, this method allows manufacturers to produce exceptionally precise and reliable components. The non-conductive properties of many plastics used in injection molding further enhance their appeal in electronic applications.
3. Consumer Goods
From toys to household items, consumer goods often benefit from injection molding. The scalability of production and quality assurance offered by injection molded plastic manufacturers help brands maintain competitive pricing and high standards, essential in consumer markets.
4. Medical Devices
The medical sector requires high-precision parts that also adhere to strict hygiene standards. Injection molding can produce intricate designs with smooth surfaces, ideal for surgical instruments or enclosures for sensitive equipment. Moreover, manufacturers can select biocompatible materials for medical applications.
5. Packaging
Injection molding allows for the creation of various packaging solutions, from bottles to containers. These products can be tailored to protect their contents while maintaining an appealing design, crucial for marketability.
Choosing the Right Injection Molded Plastic Manufacturer
When selecting a partner among the many injection molded plastic manufacturers, several factors should be considered:
- Experience: Look for manufacturers with a proven track record in the industry relevant to your needs.
- Quality Certifications: Ensure the manufacturer has the necessary certifications, such as ISO 9001, to guarantee quality assurance in their processes.
- Technology: The latest technology can greatly impact the efficiency and quality of production. Ensure the manufacturer invests in modern machinery and techniques.
- Customer Service: A responsive and knowledgeable team can make the process smoother and more effective.
- Customization: Many projects may require specific modifications. Look for manufacturers that offer customization solutions.
Future Trends in Injection Molding
The field of injection molding is continually evolving, shaped by technological advances and market demands. Here are some future trends to watch:
1. Sustainable Practices
With growing environmental concerns, many injection molded plastic manufacturers are adopting sustainable practices. This includes using recycled materials and developing eco-friendly products. Innovations in biodegradable plastics are also paving the way for a greener future in manufacturing.
2. Advancements in Technology
The integration of smart technology and industry 4.0 practices is revolutionizing injection molding. Automation, AI, and the Internet of Things (IoT) are enhancing production efficiency, predictability, and quality control.
3. Customization and Rapid Prototyping
The demand for customized products is increasing. Manufacturers are adopting rapid prototyping technologies to allow for quick iterations of design. This flexibility is leading to more innovative product developments tailored to specific consumer needs.
4. Collaboration with Design Teams
As companies increasingly recognize the importance of design in product development, injection molded plastic manufacturers are collaborating more closely with design teams. This partnership leads to products that are not only functional but also aesthetically pleasing.
Conclusion
Injection molded plastic manufacturers are at the forefront of modern manufacturing, offering significant advantages including cost-efficiency, versatility, and the ability to produce complex designs. The impact of their products is felt across numerous industries, from automotive to medical devices. As technology advances and sustainability becomes a crucial focus, the potential for growth in this sector will only increase.
Choosing the right partner among injection molded plastic manufacturers is essential for businesses looking to innovate and thrive in competitive markets. By understanding the benefits, processes, and future trends, companies can harness the power of injection molding to enhance their product offerings and meet consumer demands effectively.
As you consider your options, remember that aligning with an experienced manufacturer that prioritizes quality, technology, and customer service can set your business on the path to success. The world of injection molded plastics is vast and dynamic, making it a key player in the manufacturing landscape.